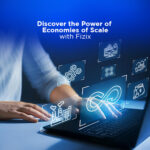
Discover the Power of Economies of Scale with Fizix
January 24, 2025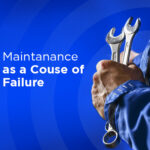
Maintanance as a Couse of Failure
January 24, 2025In the technological landscape, smart sensors stand out as pivotal tools in redefining maintenance. These tiny yet powerful devices are turning the tables on traditional maintenance methods, paving the way for more efficient, predictive strategies. In this blog, we’ll explore how smart sensors are leading a maintenance revolution across various industries.
1. The Rise of Smart Sensors in Industry
In the industrial world, maintenance is key to ensuring uninterrupted operations. Smart sensors, equipped with the ability to process and communicate data, have brought about a radical change. They constantly monitor the condition of machinery, detecting anomalies that could lead to breakdowns. By analyzing vibration, temperature, and other critical parameters, these sensors can alert maintenance teams about potential issues, allowing for swift action to prevent downtime. This proactive approach not only saves costs but also enhances the lifespan of equipment.
2. Predictive Maintenance: A New Paradigm
Gone are the days of waiting for a machine to break down before fixing it. Predictive maintenance, empowered by smart sensors, is about foreseeing problems before they occur. These sensors collect data over time, feeding it into advanced algorithms that predict when a machine might fail. This method is particularly beneficial in industries where equipment failures can have severe consequences, like in aerospace or manufacturing. By predicting and preventing failures, industries can save millions in repair costs, reduce safety risks, and maintain a steady flow of operations.
3. Smart Sensors in Everyday Life
Smart sensors have found their way into our daily lives, making them safer and more convenient. In smart homes, these sensors control lighting, heating, and security systems, adapting to our habits for optimal comfort and energy efficiency. In wearable technology, they monitor health metrics such as heart rate and activity levels, playing a crucial role in personal healthcare. Even in automobiles, smart sensors contribute to safer driving experiences by assisting with parking, collision avoidance, and monitoring vehicle health.
Conclusion
The impact of smart sensors on maintenance strategies is profound and far-reaching. From revolutionizing industrial maintenance to seamlessly integrating into our daily lives, they represent a significant stride towards a future where efficiency, safety, and foresight are paramount. As we continue to embrace these innovations, the role of smart sensors in maintenance will undoubtedly expand, leading us into an era of unparalleled operational intelligence.
Scenario: Smart Sensor-Enabled Predictive Maintenance in a Manufacturing Plant
Imagine a large automotive manufacturing plant where precision and uptime are crucial. The plant is equipped with numerous high-speed assembly robots and conveyor systems, all vital to maintaining production efficiency.
Implementation of Smart Sensors: The plant integrates smart sensors into its key machinery. These sensors are capable of measuring a range of parameters such as vibration, temperature and ultrasound frequencies.
Operational Scenario: One of the assembly robots, which is critical to the production line, begins exhibiting slight variations in vibration patterns. This change is subtle, not immediately noticeable to human operators or traditional monitoring systems.
Smart Sensor Action: The smart sensors attached to this robot continuously collect and analyze vibration data. Utilizing machine learning algorithms, the sensors detect the abnormal pattern that deviates from the established baseline. This anomaly suggests a potential bearing failure in the robot’s arm joint, which could lead to a sudden breakdown if left unaddressed.
Alert and Predictive Maintenance: The smart sensor system immediately sends an alert to the plant’s maintenance team, providing detailed data about the potential issue. The alert includes a predictive analysis, estimating that the bearing will fail within the next 72 hours if no action is taken.
Preventive Action: Armed with this information, the maintenance team schedules a repair operation during off-peak hours. They replace the at-risk bearing, avoiding unexpected downtime. The repair is quick and efficient, as the team was able to prepare in advance, having all necessary parts and tools ready.
Outcome: Thanks to the smart sensors’ predictive capabilities, what could have been a costly and disruptive breakdown, resulting in hours of lost production and high repair costs, is averted. The plant continues its operations with minimal interruption, maintaining high productivity and efficiency.
Broader Impact: This scenario exemplifies how smart sensors can revolutionize maintenance in an industrial setting.
By shifting from a reactive to a predictive maintenance model, the plant not only saves on repair costs and avoids downtime but also extends the lifespan of its equipment. This proactive approach to maintenance becomes a cornerstone of the plant’s operational strategy, ensuring it remains competitive and resilient in a fast-paced industry.