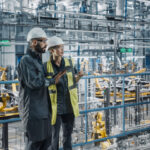
Maximizing Efficiency: The Role of Smart Sensors in Industrial Reliability
January 24, 2025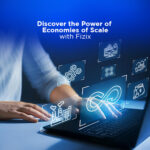
Discover the Power of Economies of Scale with Fizix
January 24, 2025Rotating equipment is vital for ensuring smooth and efficient operations in production facilities. These machines handle essential tasks like energy transfer, material movement, and process continuation. Failures in such equipment can disrupt operations, leading to production losses, higher energy use, and even safety risks or environmental damage.
Failure Modes, Effects, and Criticality Analysis (FMECA) is a systematic method for identifying and analyzing potential failures in rotating equipment. It helps improve reliability, reduce risks, and lower maintenance costs by guiding effective risk management and maintenance strategies.
FMECA Steps for Rotating Equipment
- Identifying Failure Modes: Common issues in rotating equipment include: Bearing Failure: Due to wear, poor lubrication, or mechanical stress.Shaft Misalignment: From load imbalance or thermal changes.Coupling Misalignment: Caused by improper setup or overloading.Gear Failure: Due to overloading, improper lubrication, or assembly errors.Vibration Issues: Caused by imbalance or resonance.Lubrication Problems: Such as insufficient, contaminated, or incorrect lubricant use.
- Evaluating Failure Effects: Each failure mode’s impact on the system is analyzed, such as: Bearing Failure: Leads to downtime, increased energy costs, and secondary damage.Gear Failure: Results in long repair times and potential safety risks.Vibration Issues: Affects product quality and may cause additional damage.
- Criticality Analysis: Failures are prioritized by evaluating: Probability: How often the failure occurs.Severity: The level of disruption caused.Detectability: How easily it can be identified early.
Benefits of FMECA
- Risk Reduction: Focuses maintenance on critical components.
- Improved Maintenance Planning: Enables preventive and predictive strategies.
- Resource Efficiency: Allocates resources to the most critical areas.
- Uninterrupted Operations: Minimizes disruptions and downtime.
- Conclusion FMECA is an effective tool for managing rotating equipment. It identifies risks, optimizes maintenance, and enhances operational reliability. By using FMECA, production facilities can reduce failure risks, improve efficiency, and achieve sustainable operations.